The Woolmark Company has collaborated with knitting machine company Shima Seiki Italia S.p.A and four Merino wool yarn manufacturers – Tollegno 1900, Zegna Baruffa Lane Borgosesia, Südwolle Group and Loro Piana Yarns – to create a new capsule collection inspired by protection wear.
The collection comprises four outfits that highlight the suitability of Merino wool as the ultimate natural and performance fibre suitable for a modern, urban look. The garments are a showcase of the latest knitting technology from Shima Seiki as well as Woolmark-certified Merino wool yarns.
BENEFITS OF WOOL IN PROTECTION WEAR
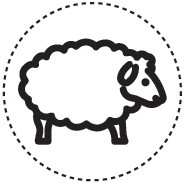
NATURAL
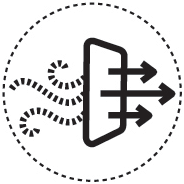
BREATHABILITY
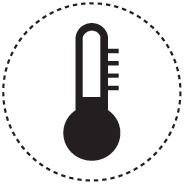
THERMOREGULATING
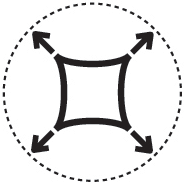
STRENGTH
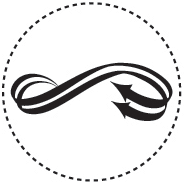
ELASTICITY
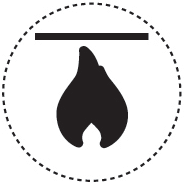
FIRE RESISTANCE
Reversible hoodie and trousers made using yarns from Tollegno 1900
This reversible zipped hoodie and trousers were made using Tollegno 1900’s 19.5 micron Harmony 4.0, NM 2/48 high twist Merino wool yarn that provides superior softness, high elasticity, minimum hairiness and pilling, and water resistance.
The reversable hoodie was knitted on a Shima Seiki WHOLEGARMENT® flat knit machine, MACH2XS 15-gauge, which allows a double knitting of the single pieces, combining wool and technical yarn, to create a different look on each side of the garment. The trousers were knitted using Shima Seiki's SRY 14-gauge flat knit machine using the inlay technology combining wool and technical yarns to provide a more compact fabric. The garments are machine washable and suitable for tumble drying.
Photo credit: Kevin Rashid Giaquinto
Jacket coat made using yarns from Zegna Baruffa Lane Borgosesia
This jacket coat was made using Zegna Baruffa Lane Borgosesia’s 19.5 micron H2DRY K-WOOL, NM 2/60 high twist Merino wool yarn to provide natural elasticity, enhanced breathability and moisture management.
It was knitted using Shima Seiki's SRY 14-gauge flat knit machine. Kevlar® yarn is used on the front, back and elbows to provide protection and high resistance. The coat is machine washable and suitable for tumble drying.
Photo credit: Kevin Rashid Giaquinto
Jacket and trousers made using yarns from Südwolle Group
This jacket and trousers were made using Südwolle’s Omega Twist Spinning Technology
OTW® Grapes NM 2/30 yarn, which comprises 48.5% 22.5 micron Merino wool to provide a clean surface that is soft to touch with minimum hairiness and pilling. The yarn is blended with 48.5% Cordura® polyamide 6.6 and 3% polyamide 6 filament to enhance the wool’s durability, abrasion resistance and strength.
The jacket was knitted using Shima Seiki's SRY 14-gauge flat knit machine, inlayed with inserts of Kevlar® yarn in double knit on the breast and elbows for abrasion resistance with details providing high visibility. The trousers are also inlayed with Kevlar® yarn for protection and abrasion resistance on the knees, with details providing high visibility. The garments are machine washable and suitable for tumble drying.
Photo credit: Kevin Rashid Giaquinto
Dress made using yarns from Loro Piana Yarns
This dress was knitted, using Loro Piana Yarns’ ultrasoft 15.5 micron Ice Wish®, NM 2/30 Merino wool yarn, on a Shima Seiki WHOLEGARMENT® flat knit machine, MACH2XS 15-gauge, to produce a completely seam-free garment. The side split and a split behind the neck are created directly by the WHOLEGARMENT® knitting machine.
High visibility yarn is directly inlayed on the front and back to also add strength and rigidity.
Photo credit: Kevin Rashid Giaquinto
The new capsule collection will provide an inspiration for manufacturers and brands along the textile supply chain to develop innovative garments not only in the protective workwear market but also for the urban fashion sector popular with millennials.
The concept for the collection was the idea of the global authority on wool, The Woolmark Company, and Creative Director of Shima Seiki Italia, Vittorio Branchizio. It was inspired by the Workwear ‘Protection Wear’ theme in The Woolmark Company’s The Wool Lab sourcing guide and aligns with the trend towards workwear-inspired designs at the latest fashion shows.
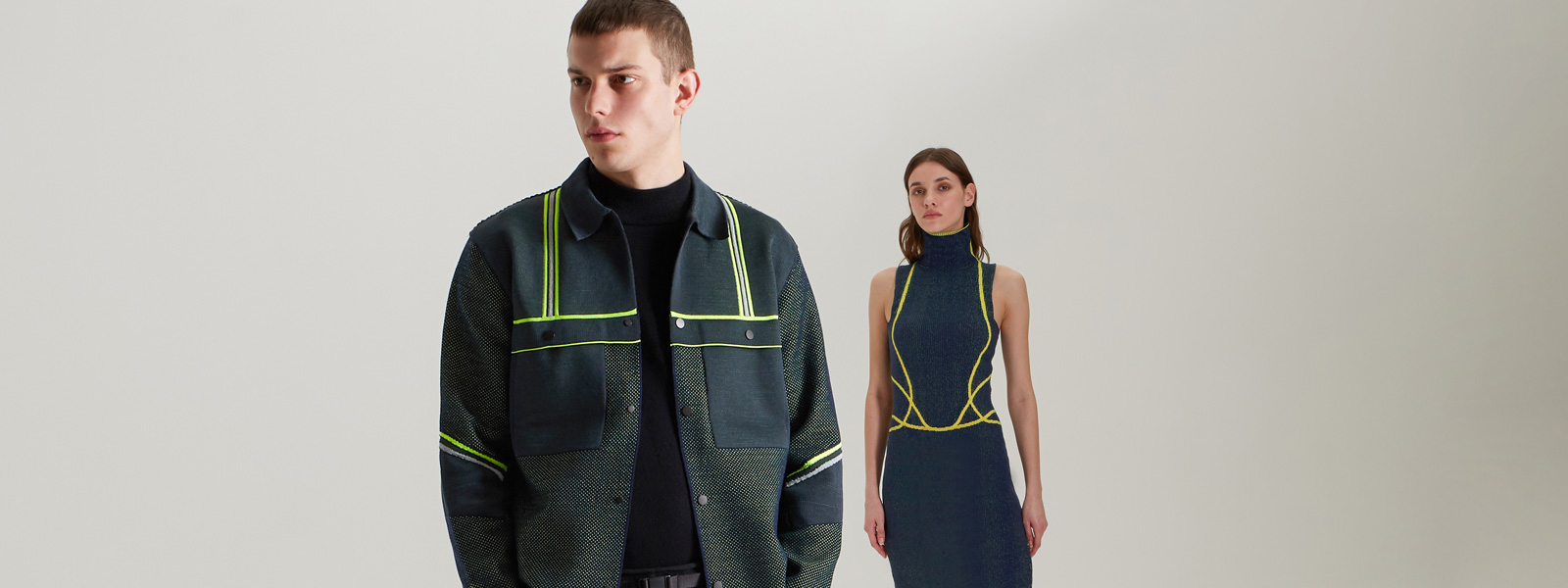
“Changes in the market have led to a new desire for practical and durable clothing that provides a level of safety and utility, while retaining a stylish aesthetic,” said The Woolmark Company’s Research & Development Manager for Europe, Birgit Gahlen.
“Merino wool not only has the eco-benefits of being a natural, biodegradable and renewable fibre, but it also has many performance advantages such as breathability, moisture management, insulation, elasticity, comfort and durability. This collection highlights the positive eco-credentials of Merino wool as well as its technical strengths and modern design.”
While comprised predominantly of Merino wool, the outfits in the collection also include some other technical yarns, such as Cordura® and Kevlar®, which demonstrates Merino wool’s versatility for blending.
The garments were knitted on Shima Seiki machines to produce garments that have a high performance and innovative aesthetic.
“The synergies that arise by creating these projects are very important,” said Vittorio Branchizio. “The collaboration between The Woolmark Company and Shima Seiki Italia enables us to carry out innovation and research projects throughout the supply chain to showcase the enormous potential of Merino wool.
“The collaboration between The Woolmark Company and Shima Seiki Italia enables us to carry out innovation and research projects throughout the supply chain to showcase the enormous potential of Merino wool."

“We start our design process directly with the wool fibre and mix it to create new materials and structures that with the Shima Seiki technology we bring to maximum expression. Using all the programming processes on Shima Seiki Apex software, both 3D and CAD, we are able to minimise yarn wastage and achieve our desired goal.”
The production process is an environmentally friendly one that avoids the traditional cut and sew technique and uses exactly the correct quantity of yarn, thereby resulting in less yarn wastage than traditional garment manufacturing. In this particular project, all the yarn suppliers were European which helped minimise its environmental and financial costs of transportation.
The capsule collection comprises four outfits, each incorporating a different Woolmark-certified Merino wool yarn.