Wool is manufactured from the raw fibre into yarn via either the woollen or worsted processing system. Yarn is then manufactured into knitted and woven wool textiles and products.
Most Australian wool is used for the manufacture of apparel products. The process of turning the raw wool fibre into fabric involves the production of yarn via two main manufacturing methods: the worsted system and the woollen system.

Discover the journey of woollen and worsted yarn
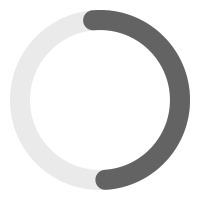
What is woollen yarn?
Woollen yarn is usually created from the shorter fibres of the sheep's fleece. These wool fibres vary more in diameter and length. Woollen yarn is used to make thick, heavyweight woven or knitted garments. These fabrics are ideal for warm winter jackets or sweaters.
Blending
Blending, which can occur at several points during early-stage processing, combines wool from various bales to ensure the resultant top, yarn (and ultimately the wool product) is as even and uniform as possible across all characteristics throughout its entire length.
Learn more in the Introduction to wool processing course.
Scouring
Before wool can be processed into yarn, it must be washed (scoured) to remove the bulk of contaminants from the raw fibre including:
- Dirt
- Wool wax
- Salts from suint (sweat)
- Non-wool protein material
- Skin pieces
Scouring involves:
- Washing wool in a detergent solution
- Rinsing the fibres
- Drying the clean wool.
During scouring wool is passed through a series of bowls containing water and detergent.
Learn more in the Raw wool scouring course.
Carbonising
Carbonising uses sulphuric acid to remove vegetable matter, such as burrs or seeds, when levels exceed 5% of the weight of the wool.
Although much of this vegetable matter could be removed through the process of combing, because combing is not used in the woollen processing route, carbonising is often required.
Learn more in the Worsted and woollen spinning course.
Woollen carding
The carding action in woollen carding is similar to worsted carding where the wool is fed into the carding machine where wire-covered rollers separate the fibres, except:
- mixing of the wool (blending) is encouraged by cross-lapping the sliver formed and re-carding the cross-lapped layer in the second part of the card
- at the end of the card, instead of being wound into a can as a single sliver ready for gilling the web is split into narrow strips called ‘slubbings’, ready for spinning.
Learn more in the Worsted and woollen spinning course.
Woollen spinning
Woollen yarns are spun using almost the same principles as the process undertaken for worsted spinning.
The differences are:
- the slubbings from the woollen card are given only a little stretch before twisting — just enough to maintain cohesion. This contrasts to the 20–30 times stretch used in worsted spinning
- a false twister is often used to give the slubbing strength, so it survives the spinning process.
Learn more in the Worsted and woollen spinning course.
Dyeing
Dyeing can occur at several points during the wool manufacturing pipeline depending on whether the wool goes through the woollen or worsted process. Wool can be dyed at the fibre, yarn, fabric or garment stage.
Learn more about dyeing wool in the Dyeing of wool course on the Woolmark Learning Centre.
Knitting
Knitting is a fabric-forming technology that has been used for thousands of years. It can be used to create fabrics, which can come off the machine as fabric to be cut or as shaped pattern pieces and whole garments. Knitting can be carried out with:
- simple technology (i.e. hand knitting needles)
- sophisticated computer-controlled knitting machines.
Learn more about knitting in the Knitwear Design and Make course on the Woolmark Learning Centre.
Weaving
Weaving is the process of interlacing warp and weft yarns in a weaving machine, or loom. It is used extensively to manufacture fabrics used to create apparel and interior textiles. Weaving can use:
- simple frames to hold the threads
- complex weaving machines under computer control.
Learn more about weaving in the Woven textile design and production course on the Woolmark Learning Centre.
Non-woven fabric
The production of non-woven fabrics requires methods to form layers of fibres into coherent fabrics without the need to spin yarns. Although most non-woven methods of fabric formation are relatively new, one of the techniques available to make non-woven wool fabrics — felting — has been used for many years and used by many early cultures.
Learn more about knitting in the Introduction to wool processing course on the Woolmark Learning Centre.
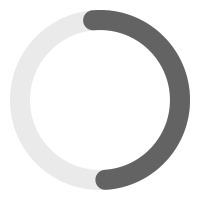
What is worsted yarn?
Worsted yarn mainly uses the highest quality fleece wool obtained during shearing. Fleece wool generally contains the longest wool fibres, which vary less in diameter and length. Worsted yarn is used to make flatter, lighter and smoother fabrics such as those used for traditional tailoring.
Blending
Blending, which can occur at several points during early-stage processing, combines wool from various bales to ensure the resultant top, yarn (and ultimately the wool product) is as even and uniform as possible across all characteristics throughout its entire length.
Learn more in the Introduction to wool processing course.
Scouring
Before wool can be processed into yarn, it must be washed (scoured) to remove the bulk of contaminants from the raw fibre including:
- Dirt
- Wool wax
- Salts from suint (sweat)
- Non-wool protein material
- Skin pieces
Scouring involves:
- Washing wool in a detergent solution
- Rinsing the fibres
- Drying the clean wool.
During scouring wool is passed through a series of bowls containing water and detergent.
Learn more in the Raw wool scouring course.
Worsted carding
The carding process is where the wool is fed into the carding machine where wire-covered rollers separate the fibres to:
- Untangle the locks and clumps of wool and separate the wool into individual fibres
- Remove vegetable matter
- Partially align the fibres
- Form the fibres into a sliver (untwisted, rope-like strands of fibre).
Learn more in the Worsted and woollen spinning course.
Gilling
Before a worsted yarn can be spun, the sliver needs to be ‘gilled’ (to straighten the fibres by stretching the sliver) and combed to remove the short fibres (noils) and any vegetable matter.
Gilling is done to:
- Align the fibres in a parallel direction so they can pass through the very fine comb on the combing machine.
- Produce a sliver with a more uniform weight per course length.
- Add processing aids to the fibre.
Learn more in the Worsted top-making course.
Combing
Following gilling, the combing process removes vegetable matter, nep and short fibres (noils).
The process of combing is as follows:
- A fringe of clamped fibres is presented to a pinned cylinder, which straightens the long fibres and removes short fibres, nep and vegetable matter.
- The cleaned fringe is then gripped and drawn through a single strip of very fine pins to complete the cleaning of the back end of the fibres.
- The fringes are recombined to form a sliver.
After combing, the sliver is re-gilled 2–3 times. The sliver is now known as ‘top’.
Learn more in the Worsted top-making course.
Roving
Before the newly formed wool top can enter the spinning stage, it has to be made some 40 times thinner by ‘drawing’ it down into a fine sliver, called a roving. The roving is then ‘spun’ to form a worsted yarn.
Learn more in the Worsted top-making course.
Worsted spinning
The purpose of spinning is to:
- Extend the roving into a continuous strand of yarn, which has a specified fineness, indicated by a count number
- Insert sufficient twist into the yarn to bind the fibres together, so it is strong enough to withstand the strains of subsequent processing.
There are several types of spinning:
- Ring spinning — most common for the worsted and woollen industries
- Mule spinning — sometimes used in the woollen industry
- Open-end short-staple spinning — used for cotton
Learn more in the Worsted and woollen spinning course.
Dyeing
Dyeing can occur at several points during the wool manufacturing pipeline depending on whether the wool goes through the woollen or worsted process. Wool can be dyed at the fibre, yarn, fabric or garment stage.
Learn more about dyeing wool in the Dyeing of wool course on the Woolmark Learning Centre.
Knitting
Knitting is a fabric-forming technology that has been used for thousands of years. It can be used to create fabrics, which can come off the machine as fabric to be cut or as shaped pattern pieces and whole garments. Knitting can be carried out with:
- simple technology (i.e. hand knitting needles)
- sophisticated computer-controlled knitting machines.
Learn more about knitting in the Knitwear Design and Make course on the Woolmark Learning Centre.
Weaving
Weaving is the process of interlacing warp and weft yarns in a weaving machine, or loom. It is used extensively to manufacture fabrics used to create apparel and interior textiles. Weaving can use:
- simple frames to hold the threads
- complex weaving machines under computer control.
Learn more about knitting in the Introduction to wool processing course on the Woolmark Learning Centre.
Non-woven fabric
The production of non-woven fabrics requires methods to form layers of fibres into coherent fabrics without the need to spin yarns. Although most non-woven methods of fabric formation are relatively new, one of the techniques available to make non-woven wool fabrics — felting — has been used for many years and used by many early cultures.
Learn more about knitting in the Introduction to wool processing course on the Woolmark Learning Centre.
Woolmark Learning Centre
Free online training
Learn more about Wool processing and manufacturing on the Woolmark Learning Centre. Free to access, these intuitive online courses will further your education on wool fibre science, how wool is processed and how fabrics are finished and dyed.